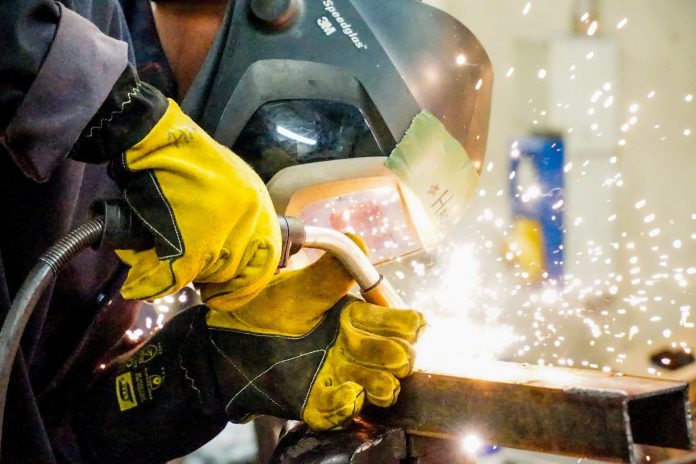
ABERDEEN PROVING GROUND: To prepare for the future battlefield, the Army has defined a concept for its next generation of combat vehicles. These vehicles, encompassing a family of new platforms, will have advanced capabilities to ensure continued overmatch against adversaries for decades and beyond. Enhanced survivability is critical for these vehicles, and will be enabled by improved designs, materials and manufacturing processes.
Today, combat vehicle hulls are typically fabricated from thick armor plates that are manually welded together. Numerous weld passes are required at each weld seam, so it can take several days to weld together a base vehicle hull. While advanced welding technologies to reduce the number of weld passes have been tested and proven, many are deemed too hazardous to be performed by hand.
To improve the quality of combat vehicle weldments and reduce fabrication time, the U.S. Army Combat Capabilities Development Command Manufacturing Technology program funded a project to develop a robotic manufacturing cell to automate heavy weld operations for combat vehicles.
This cell is equipped with an advanced welding technology called High Energy Buried Arc Welding, which enables high-quality, thick-plate welds with minimal passes. The cell also contains a high-capacity, multi-axis positioning system that can manipulate multi-ton vehicle structures into ideal welding positions.
The robotic weld cell has multiple benefits for next generation combat vehicles: the quality and performance of weldments is higher, which results in better vehicle protection; and the automation reduces welding time by nearly 80 percent, which will help the Army meet its critical delivery requirements.
“The system is operational and currently being controlled manually,” said Megan Lynch, ManTech project officer. “We are still in the learning and debugging phase. Getting to full operational capability will be a process, but we are on track to get there by FY21.
“Initially, the robot was operated with a thicker weld wire than what is currently being used, but technical difficulties required us to take a step back and go to a thinner wire. We are now ready to start looking into a thicker wire again,” Lynch said.
Using a thicker weld wire enables a higher weld deposition rate and fewer passes. This will reduce welding time and potentially increase weld performance, two goals of the project. Initial testing, however, showed the targeted weld wire size was too thick to feed and cool properly in the cell’s existing design. The weld wire optimization study planned for FY20 will focus on how to resolve these issues.
The development, integration, and prove-out of this robotic weld cell was achieved in partnership with BAE Systems in support of the Armored Multi-Purpose Vehicle program, which is the robotic weld cell’s first Army customer.
“By using the robotic welding cell technology funded by the Army’s ManTech program, we were able to execute and transition the Armored Multi-Purpose Vehicle program from the Engineering Manufacturing Development phase to Milestone C. We worked closely with the ManTech team, which provided additional resources to support the Army’s first new combat vehicle production program in more than 30 years,” said Lt. Col. Ryan Howell, Product Manager, Program Executive Office Ground Combat Systems.
Once transitioned, the robotic weld cell is expected to perform approximately 70 percent of the heavy welds for the AMPV hull and reduce vehicle weld time up to 80 percent. These changes will help the AMPV program and the Army meet their fielding goals.
The U.S. Army Combat Capabilities Development Command (CCDC), formerly known as the U.S. Army Research, Development and Engineering Command (RDECOM), has the mission to lead in the discovery, development and delivery of the technology-based capabilities required to make Soldiers more lethal to win our Nation’s wars and come home safely. The command collaborates across the Future Force Modernization Enterprise and its own global network of domestic and international partners in academia, industry and other government agencies to accomplish this mission. CCDC is a major subordinate command of the U.S. Army Futures Command.
from Defense News by DefenceTalk.com https://ift.tt/37B1M1I
via Defense News
No comments: