By ASHOK K. BAWEJA
Former Chairman & Managing Director
Hindustan Aeronautics Ltd (HAL)
There has been a debate on the Naval Utility Helicopter (NUH) with statements made by the former Chief of Naval Staff and retired Naval officers and response by Chairman HAL and retired HAL executives associated with the ALH programme.
The point of view of the naval officers has been that the Dhruv naval nariant is patently unsuitable because of lack of acceptable blade folding feature, and indifference of HAL to the Indian Navy’s specific requirements. I would quote liberally from technical papers and interviews of a number of test pilots from the services at HAL who have been involved with the initial design, development, flight testing and subsequent flying after certification of the Dhruv. But first, some background.
The origins of the ALH project are in the IAF-Army requirements specified in Air Staff Requirements (ASR) 2/79 which was released in May 1979 and a related Navy Staff Requirement (NSR) AO/4721/1978, released in 1985 for the Navy variant. The ambitious requirements given in the ASR and NSR were for a common base platform capable of performing a sweeping range of roles at altitudes ranging from sea level to 6 km (19,500 ft) pressure altitude, at high temperatures.
Against these very high benchmarks and somewhat sweeping and futuristic expectations, the Government set up a Negotiations Committee to explore the possibility of collaboration with Aerospatiale (France) or MBB (Germany). Thereafter, HAL was tasked to develop the helicopter and Germany’s Messerschmitt-Bölkow-Blohm (MBB) was contracted in July 1984 to act as a design consultant and collaborative partner for the program for a period of 10 years. The first prototype flew in August 1992. Whereas the testing for the Army-IAF variant progressed steadily albeit with delays, the Navy prototype which flew with US (Allied Signal) CTS-800 engines ran into severe delays. This was mainly when the US withdrew these engines in the sweeping embargo enforced following the nuclear tests in Pokhran, 1998.
While hindsight is always 6×6, the indisputable fact is that the combination of spectrum-sweeping performance and role requirements that were demanded from a single platform and certain design options that were incorporated, created extremely severe hurdles to practical implementation.
Whereas today one is not aware of the imperatives that influenced the drafting of the staff requirements in the late 1970s, or the decision of the Negotiations Committee in accepting the recommendations of MBB in the early 1980s, the fact remains that some of the futuristic design options put forth by MBB were initially resounding failures. The project that was supposed to have progressed smoothly under the tutelage of advanced German technology, instead stumbled badly to almost a point of no-return and required extreme effort by our indigenous teams to recover, re-develop from basic design stages and optimise for production.
To be only fair, the ALH owes its excellent performance to the then futuristic requirements that were specified by the armed forces. The demand for extreme excellence at specific performance points and in some roles is justified and even welcome, as that is what makes the product unique.
However, the problem creeps in when the requirements are at far too many points spread across the spectrum and are also beyond the range of contemporary technology for a single platform. Whereas the IAF-Army and Navy had issued separate ASRs, the fact remained that the base platform was common and the IAF-Army ASR also acknowledged the fact. Especially when seen together, some of the requirements were clearly contradictory and beyond the reach of contemporary technology for a single platform.
For example, the cabin size required to accommodate all the weaponry and sensors for the Navy variant would require a larger and heavier airframe, with larger rotors and engines that in turn would put beyond reach the specified performance and payload required for 6 km altitude for the IAF-Army utility role.
The ALH (or Dhruv) was an ambitious first-time project to design and build a common helicopter platform catering to all the requirements of the Army, Navy and IAF. The roles it was envisaged to fulfil in different variants were extremely varied, ranging from landing at 6 km altitude to armed, night attack, anti-submarine, anti-surface warfare, SAR, troop carriage and utility roles. The wide range of envisaged sensors and weapons included 20 mm cannon, anti-armour missiles, torpedoes, Exocet-class missiles and depth charges.
The Army-IAF variant was to have an electronic warfare (EW) suite and advanced sighting and aiming systems and the Navy variant was to have dipping sonar, surveillance radar, sonobuoys and magnetic anomaly detector (MAD). The Navy also wanted capability to change roles in quick-time (capability to remove ASR equipment in three hours).
It is understood that when the ALH partnership was being finalised, all the three armed forces, MoD and HAL were very much part of the selection of MBB’s latest technology of rigid rotors. Navy was told right in the beginning the dimensions, performance and the capabilities of the ALH, and later on also it was repeatedly told that Sea King equipment cannot be installed on ALH and expect the performance they want from the 5.5 ton ALH .
Notwithstanding this, HAL continued with the trials and a substantial effort of HAL’s Rotary Wing R&D Centre (RWR&DC) was aimed towards naval prototype testing. To further accommodate their requirement, the trials to fly naval ALH with the drag dampers on leading and trailing edge of the alternate blades were successfully carried out. Thus the naval ALH is the only helicopter in the world with this configuration. Sonar winch, torpedo and many other trials were carried out for the Indian Navy at their behest (even though it was known that they may not accept the naval variant). The ship envelope was demonstrated on the smallest deck the Indian Navy could provide.
Incidentally the nnaval variant has a retractable under carriage, Harpoon deck lock mechanism which in turn adds to the weight of the aircraft. It is also understood that Dieter Bender, Chief Designer and Program Head from MBB, had amply given in detail what a hinge-less rigid rotor can do to all the three variants for the services.
The 3.5 g requirement and battlefield survivability for controls were the major factors affecting the design of the rotor and the rotor head. To enable ALH to make such high ‘g’ manoeuvres, the rotor had a large hinge offset which was partly accomplished by the large rotor head. The large rotor mast also accommodated the controls which passed through the centre of the main gear box (MGB).
With a large rotor head, the ALH with its blades folded became too big to manoeuvre into the ship hangars. It could enter but with inches to spare only. As for the mission equipment, the contemporary systems of that era were heavy and when fitted on the ALH the time on task required could not be met.
ALH was specifically designed for high altitude and some intensive manoeuvring which are exactly opposite to what the Indian Navy needed. Army had an Army Project Team on site actively involved in the ALH development. There was a Naval Project Office headed by Commodore rank officer who had all the opportunity to bring forward to Naval HQ what the ALH in its then variant could or could not do.
HAL had more than enough challenges in meeting development challenges of gear box, vibrations, vertical oscillations, high altitude performance with respect to payload, tail rotor actuators, production of composite rotors , collectors gears, MGB cracks, short life ARIS springs and a host of others. It would have still been opportune at that point in time when tasks pertaining to the naval version were being carried out for the Indian Navy to take a hard call and interact with HAL to define an aircraft which would meet their requirements of blade fold, time on task with two torpedoes etc.
I don’t recall any discussion on these lines although being on the Board of HAL for 11 years.
A June 20 article on Livefist by Wg Cdr Anil Bhambani is relevant in entirety, commencing, with the section of test crew engagement with the Dhruv. I have seen and encountered an exceptionally high involvement of Army and IAF pilots and test engineers participating in the flight trials, keeping their Service HQs updated and provide service inputs so that they could be incorporated. I recall often rather ‘pointed’ feedback including a most awkward incident when the collective came loose.
It could be mentioned that HAL even then was being most proactive and, post Kargil, had proposed a dedicated attack helicopter and was also developing a Light Utility Helicopter (LUH), the latter shelved in 2002 to enable the Indian Army to import 60 (later increased to 197) 3 tonne class helicopters. The LUH was later revived and sanctioned in February 2009 and now has finished the last stage of high altitude trials recently.
It could also be said at this stage that HAL was most forthcoming in trying to find solutions. The Shakti engine development, giving multiple times the 6 km payload requirement (helicopter engines tried out were the TM 333 B, LHTEC T 800 the TM 333 -2B and finally the Shakti), the glass cockpit and active anti vibration system were all HAL initiatives.
I hasten to state that I have utmost respect for the Indian Navy for its support to indigenous design, with the Directorate of Naval Construction formed in 1954 and the Directorate of Naval Design (DND) in 1970, which has been a cornerstone for the construction of 119 warships and submarines of various types and sizes in our shipyards as of date with another 40 plus under construction. I also observed that many officers of the Indian Navy whom I met were very highly qualified with Masters to their credit.
On the aviation side I have great regard for Commodore CD Balaji the architect of the LCA Navy. My interactions with Vice Admiral Raman Puri, a champion of indigenous development (who drives only an Indian designed car) who was also on HAL’s Board as an independent Director were an education. It was his initiative and thrust that resulted in development of the TMS for the ALH as against the imported option. He did an independent study of the Jaguar DARIN II programme and made us realize what Indian organisations could achieve.
Coming now to the NUH, the current controversy is about HAL’s potential participation with the ALH Dhruv. The ALH’s suitability for the NUH requirement was addressed by Wg Cdr Anil Bhambani, who is a Test Pilot first, ex IAF (ASTE) and now at HAL. I quote him and a Chief Designer with whom I spoke recently.
BLADE FOLD
The LUH, using a segmented blade has been flown adequately. Proven blade folding on the LUH has been demonstrated to the Indian Navy. Time taken for blade fold was approximately 6 mins, well within the requirements asked for NUH. I very recently had the opportunity to see the LUH blade demonstration. It took under 6 minutes and is very doable on a ship’s deck. HAL is already in the process of making a segmented blade for the ALH which will meet the blade fold requirement of the Indian Navy.
The time required is to import the material for the blade mould, make the blade tooling, and fabricate the blade, followed by certification. There is an involved certification process for the foldable blade. It is the easiest thing for this blade design to be assessed by a naval team and provide a technology certainty forecast to Naval HQ. I am sure this review would even bring forth suggestions for tweaking and improvements.
ALL UP WEIGHT (AUW)
The Indian Navy initiated the requirement for NUH as a replacement for 3.0 ton class helicopter Chetak in 2008 and subsequently had increased the AUW limit to 5.0 tons in its NUH NSQR.
ALH Mk III with 5.75 T is under production as per present on-going contract with Indian Navy. HAL is offering a re-configured version of Mk III ALH as NUH by removing some systems which are not required for NUH (rear main tank, surveillance radar, sonar/sonics, conventional VUHF system and high intensity strobe light) while adding some other systems (two segment blade folding, tail boom folding, software defined radio, torpedo, slewing SL, weather radar, weight reduced LRUs) to meet NUH NSQR including performance and mission requirements within a truncated AUW of 5T.
However, as the basic ALH platform is capable of an AUW of 5.75 T, Navy will have the flexibility to carry additional payload of 750 kgs or have longer range/endurance in certain missions. In comparison to the 4.5 T AUW AS365MBe Panther (which may well be the one the Indian Navy might end up with), the ALH will thus offer the Indian Navy the flexibility to add 1.25 T of useful load (fuel or mission payload) in case a mission so demands. This is a valuable option which the Indian Navy seems to be ignoring at this point of time.
RANGE AND ENDURANCE
Range and endurance for all NSQR missions (SAR, CASEVAC, communication duties, and sub-surface targeting) will be met or exceeded by the ALH being offered in the NUH configuration. HAL is also working on tail boom folding. With these in place the stowed dimensions of the ALH would meet the Indian Navy criteria. A two blade fold is an interim option, which was evaluated in the past jointly with Navy. Most of the mission equipment of the NUH has already been tried out and certified on the Dhruv.
KEY BENEFITS OF ALH AS DHRUV
Initial cost to Indian Navy:
- Acquisition of NUH from HAL will eliminate the cost of new/additional production infrastructure to be incurred by the Strategic Partner, the complete set of tools, tigs, testers, etc. to be supplied by the OEM and the one-time license fee (or royalty) payable to the foreign OEM if the SP route is adopted. The consolidated financial outlays for the above three cost elements will be very substantial.
- Commonality with the existing fleet of Mk I ALH and the new 16 Mk III ALH under acquisition by Indian Navy. Infrastructure set-up already available at naval bases for MRO and ground support will eliminate additional investment cost compared to an NUH from a foreign OEM.
- Zero Transfer of Tech (ToT) Cost: Since the ALH-based NUH is conceived, designed and developed by HAL, there is no necessity for any ToT, and thus a substantial amount of foreign exchange which will otherwise be payable as ToT charges, can be saved.
- Platform Upgrade: HAL is capable of handling any additional requirement of change in specification and unilateral upgrades to cater to any emerging requirement of Indian Navy for its ship and shore based operations. As HAL is the owner of the design IP, any new weapons or sensors, indigenous or otherwise, can be integrated without much effort or involvement of foreign OEMs. A helicopter from a foreign OEM will bear an enormous cost for upgrades as design ToT will not be available with the Indian Navy.
- Obsolescence Management: The ALH-based NUH being totally an HAL product, obsolescence issues arising during the entire product life cycle can be addressed by HAL. Dependency on foreign OEMs will drain foreign exchange by way of enormous cost to be paid to foreign OEMs for obsolescence management.
Potential competitors in the NUH contest arelikely to be Panther and H145M (both from Airbus Helicopters), Sirkorsky S76D and Russian Ka226T. There is a high possibility that Panther (AS365MBe) from Airbus Helicopters of 4.5 ton AUW could end up as the potential single vendor, leaving the other helicopter proposals rejected due to technical non-compliances. Then a question may arise “Is it that the 5 Ton AUW limit for NUH was tailored to suit a particular helicopter?”
HAL has good experience in integration of weapon systems — WSI-ALH (Rudra), Jaguar DARIN II and III and the LCH. A key point is that with the NUH at a preliminary enquiry stage, by the time the RFP is issued, offers, received evaluation , negotiations, contract placed, a few years would pass. All the desired features of blade fold, tail boom folding, additional weapons and systems could be integrated, certified and even a batch of production standard aircraft kept ready for delivery, by the time the process of selection is finished and an order placed.
My understanding is that HAL capacity for the Dhruv airframe is about 40 to 48 sets annually, having sanctioned the funding for that level of tooling, jig structures and manufacture of composite parts.
Coming now to the observations of the former Chief of Naval Staff, also an aviator and other retired naval officers. The observations made on the Naval LCA, development of the Kaveri are bang on and I could not agree with him more. In regard to HAL, it is painful to hear. Maybe as an institution or somebody individually at HAL, were not correct with the Indian Navy or him, leading to the current observations.
Maybe HAL can close out the observations of Admiral Arun Prakash and invite him and other top naval officers and demonstrate the LCH, LUH, WSI- ALH Rudra, HTT-40, LCA, and other products.
R& D iniatitives of HAL
I went over the comments of Commander Yashodhan Marathe here on Livefist on June 10. Yes many are relevant and chronichled in detail. The underlying message is that HAL should have figured out all the non-conformances and addressed them in design stage itself.
“I actually casually asked some of the designers whether they had ever worked on, or closely studied any other existing type of helicopter, to see the crucial design issues and other small modifications or attention to detail they had done. No, was the answer,” says Commander Marathe.
I ask, where would the HAL designers go for experience in helicopter design? Eurocopter, Bell , Augusta Westland? Desirable but not possible. Which company in the world would give exposure to design aspects in any product?
Another quote. “So we have to understand that if a foreign vendor with years of experience comes into India to set up shop to manufacture a helicopter, he is bound to bring with him the expertise, the precision manufacturing practices, industrial safety and everything that has made that company successful.”
It must be stated that in any private sector and foreign OEM alliance, it is highly unlikely that the foreign partner would ever bring the knowhow required for the gear boxes , transmissions and rotor blades. Nobody gives or brings critical technologies whether it is super alloys, single crystal blades, variable thrust nozzles, radar blocks, data links, optronic devices (or even the formula for Coke) and many more in which billions have been spent for development. Check out the alliance between Eurocopter and the Chinese for the EC120 as to who makes what.
It is felt in an alliance of the sort between a private sector entity in India and a foreign OEM , the assembly would be done in India and the rotor and transmission would be an OEM supply. The technology is just too critical and the investment in plant equipment prohibitive to have a meaningful return on investment if ever. It is very creditable that the private sector is exporting floor boards and cabins. The next step is surely engines or their modules, rotor blades, gearboxes, turbine blades , hot end turbine components — assuming that an OEM is willing to transfer the technology build to print and the respective boards of Indian companies coming forward with the investments.
I could go on as there are lots of snipes in the article besides the observations but this would detract from the main theme. I suppose it’s kind of fashionable to pull down your own product, especially if it’s from a public sector undertaking (PSU).
Incidentally, a good portion of the Shakti is made from raw materials along with almost every engine type of Russian or western origin flown in India of aircraft from HAL .And so also fuel, hydraulic, flight control and other systems going in an aircraft. All the not-so-good comments that have been made recently are based on the ALH of the year 2000, and out of experience of operating the limited ALH (Mk1s) that are in the Indian naval inventory. These ALH were from the LSP (Limited Series Production) line up and the initial batch of production. The LSP batch used soft tooling with fair amount of fitting and adjustments.
The aim of LSPs was to get feedback from the field once the customers start exploiting the aircraft. So what the Indian Navy encountered was no different from what the Air Force and the Army experienced. These feedback/design shortcomings/manufacturing anomalies were addressed in a systematic manner and ALH continued to mature. It is a process followed across the world and not limited to HAL alone. This remains an ongoing process and all observations that HAL gets are addressed in due course, with the armed forces remaining an integral part of the process. The benefits of the series production wherein the observations have been addressed, have been passed on to the Army and Air Force in the ALH Mk III/IV versions. However the Navy continues to hold only the Mk I (LSP) variants, hence the poor experience.
On my recent visit, I closely looked at the finish and fit of the ALHs in production. It was very good and desirable.
Yes, it is agreed that the ALH did not meet the NSQR of that era and HAL did accept the same. The NSQR was based on the Sea King (equipment payload and endurance for missions) which was and is still the pride of the Indian Navy. Incidentally it was HAL which came forward to maintain Sea King transmissions when components were denied by WHL. If a realistic assessment had been done after the design freeze of ALH, it would have been obvious that ALH would not meet the naval requirement. No flight testing was required to know that the ALH will not meet the NSQR.
The Strategic Partnership (SP) Model
The government brought in the Strategic Partnership route with the aim to promote more participation from private industries in defence acquisitions, investment by private industry in R&D as well as production facilities, while also keeping in view that assets in PSUs are fully utilised. Some companies in the private sector are doing well in building to print structures for foreign OEMs and sure in the course of time to produce and build a complete platform.
It is observed that the first SP model for C-295 is yet to take off even after several years. With a small production run of about 50+ aircraft, large investments in plant and equipment, the time frames envisaged for the ROI, it is not very difficult to figure out what would be the price of C-295 made in India as a multiple of the imported flyaway cost.
It is also not clear whether the power plant and the systems — fuel, hydraulic, flight control, avionics, et al would also be made in the country from raw materials. After all the indigenous content of at least 50/60 percent would need to be achieved.
It is estimated that just the plant for assembly of helicopters would cost about Rs 700-800 crores, not counting investments required for facilities for composite parts, gears and transmissions, rotors, engine components, undercarriage and systems. The Government has got full flexibility to take decisions which are in the interest of country and can review previous decisions.
HAL’s current Chairman & Managing Director has not questioned the SP model. However he has indicated that the current requirement of the Indian Navy could be met by ALH. With about 300 ALHs in production, the Indian content has increased to 63% by value and is more than 75% in terms of number of parts produced. HAL makes the airframe and the power plant and also some of the systems. The composite rotors, all elements of the gear box transmission and engine are made in country including many castings and forgings.
Import is done of the weapons, ECMs, electro optical pods, autopilot system, Doppler, composite materials like pre-pegs, and certain systems like flight actuators, hydraulic packs, elastomeric bearings and the like. HAL has developed more than 2000 MSMEs and 24% of the work content has been outsourced to the private industries.
All aircraft helicopters have critical and proprietary technologies.
It is not certain that in the SP Model the collaborator will ensure that this level of indigenous content would, if ever, be achieved and whether rotors, transmissions, power plant and systems would be manufactured in India or ‘’supplied’’ as a kit due to very high investments in the production facilities or because of critical technology content. With many years of interactions and alliances with all OEMs involved with Indian programmes, it is highly unlikely that there will be production levels by a joint foreign and private sector alliance to the degree, depth and content which is being expected, particularly for critical and sensitive systems of the aircraft. Think single crystal blades. The airframe being about 30 percent and the power plant and systems being about 65 percent by value.
A better solution is alliances between the public and private sector for design, development and production. The AMCA is now being planned by this route. HAL Kanpur with experience in civil airframe production should be used for the C-295.
At this juncture, I am quoting from an article by Prodyut Das, a former Professor of Mechanical Engineering at IIT Kanpur who writes on aviation subjects. I have never met him but read several of his articles on the LCA , IJT and the ALH as well doctrines of warfare published in Vayu which are technically logical, besides exhibiting an extraordinary degree of common sense giving one to say why are we not thinking of that. Here is what he wrote about the ALH:
“The ALH was a project with its own share of advanced technologies,-glass cockpit, hinge less rotors and composites. It had its share of specification changes (many after Kargil –my words) and yet the product was ready, an acceptable performer. It is the classic case of a successful project competently and quietly handled by professional engineers. The point is it was achieved by men who were the poorest paid of the state sector employees who worked 6 day 48 hour weeks and who retired without even a pension. Though no supersonics is involved, helicopters are nasty things to design.”
I spoke recently to a former mid-level officer who worked on the LCA and IJT prototype structures. He is now 73 and working in Gurugram far from his home and family in Bangalore. He is surely keen to keep himself occupied but I also suspect, his reasons for working are also financial.
As I mentioned earlier, both the LCH and LUH were proactive programs from HAL . So was the IJT (another story). HAL took over the Jaguar DARIN II upgrade from an English company contracted for the same, and delivered the production standard aircraft. As a result of the knowledge and experience gained from the Jaguar upgrade, the MiG-27M, the Sea Harrier, and later the Mirage 2000 for the air to ground role were upgraded with new systems, radars and weapons. HAL has been a most active partner in the LCA development, a classic case where multiple organisations and two Services could work together on a national programme.
The Chetak and Cheetah were re-engined and the Cheetah weaponised. The ALH was demonstrated in Chile, Berlin, Paris and at Farnborough.
On the component side, where technologies were denied, threatening the program itself, HAL developed shape memory alloys (LCA), power take off shafts (ALH), directionally solidified blades being sold at extortionate pricing, carbon fibre for making composites and many more. I am proud and am sure my former colleagues and the current management are equally so.
A lot of harsh words are also spoken by the non-aviation trolls, who probably have no clue about aircraft design, production, effort involved, costs and time frames, who read articles and see video clips, with only a single solution of privatisation and other measures for HAL, close to keel hauling.
I may mention that after close association with the private sector for several years, is it surprising that so many ex-HAL designers and engineers, who left early or after retirement are sought for the talent and knowledge that they have? After all they are not layabouts. In every field of design and engineering, people are taken from HAL and DRDO organisations to be foundations of the private sector aspirations.
Yes an organisation can always do better, constuctive criticism and observation is welcome, but sniping is not, when the varibles for both success and failure are too many.
To sum up, an Indian NUH is feasible in a much shorter time and cost to certify all the add-on features and produce a batch of aircraft , as against , selecting and finalizing a foreign vendor for which the process itself would take few years and who would further have a delivery lead time of 3-4 years. The 300th Dhruv will soon go into service and has participated in many crtitical missions. The Indian Navy would benefit from a platform where the aircraft systems are common, and in-country support is available like the powerplant, fuel, hydraulic, flight control systems avionics and other systems.
Blade fold and tail boom fold are achievable.
Ashok Kumar Baweja joined Hindustan Aeronautics Limited (HAL) as a management trainee in 1972 and rose to become Chairman in 2004. Views expressed in this column are personal.
from Livefist https://ift.tt/2Iq09wx
via Live Defense
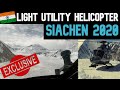
No comments: